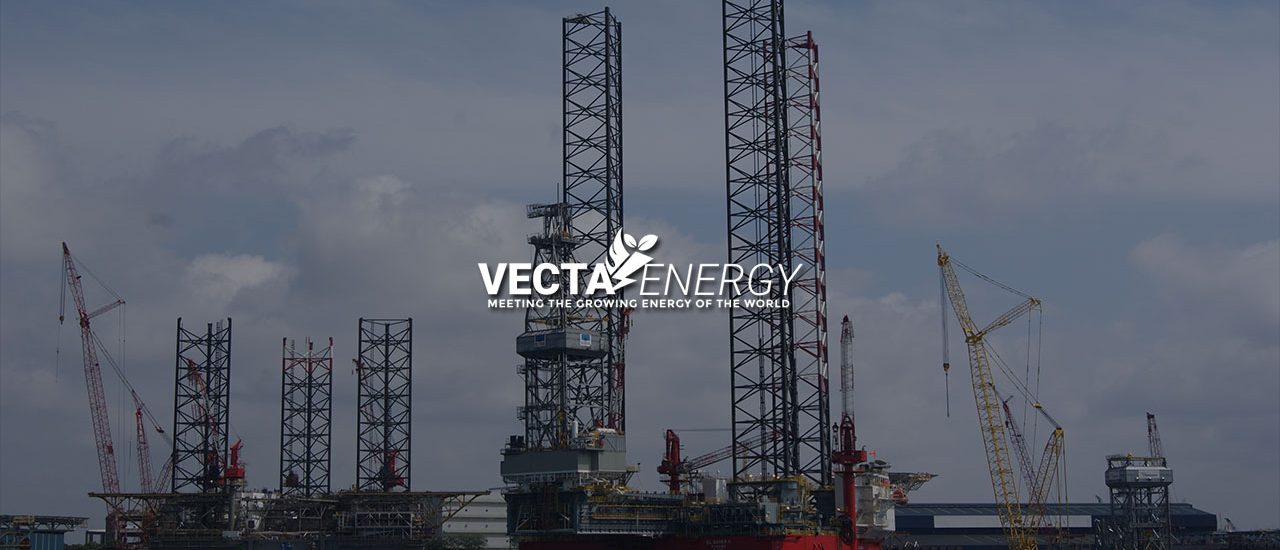
Emissions Reduction in Canada’s Oil and Gas Industry: Navigating the Pathway to a Cleaner Future
Canada’s thriving oil and gas sector faces a formidable challenge: reducing emissions, particularly fugitive emissions, while maintaining production efficiency. This challenge is shaped by both unique Canadian geography and a regulatory framework that strives to balance environmental protection with industry advancement.
A Landscape of Complexity and Opportunity
Canada’s vast landscape, characterized by remote locations and extreme weather, makes fugitive emission control an intricate endeavor. Fugitive emissions are elusive; they escape from system leaks and are harder to monitor and manage. Harnessing technology and innovation to address this challenge, the Intricate Group’s Environmental software offers real-time monitoring and tailored solutions. It’s about leveraging Canadian innovation to create lasting change in fugitive gas emissions control.
Regulatory Pathways: Aligning Goals and Responsibilities
Canada’s commitment to environmental sustainability is embodied in regulations like MSAPR Multi-sector Air Pollutant Regulations. These regulations set stringent standards for industries, focusing on multi-sector air pollutants.
Compliance requires not just understanding but anticipating regulations. The Intricate Group, with its expertise in fugitive emissions oil and gas, offers guidance and solutions that seamlessly align with regulatory expectations.
The Carbon Credit Offset Program: A Unique Approach
Canada’s Carbon Credit offset program presents a unique opportunity for oil and gas companies. By reducing emissions, they can earn credits, turning environmental responsibility into an economic advantage.
Methane: A Special Focus
Methane, as one of the potent greenhouse gases, occupies a central place in Canada’s emission reduction strategy. Both methane fugitive emissions and fugitive methane emissions need specialized monitoring and control.
Research from Environment and Climate Change Canada details the sources of fugitive emissions and the strategies employed in controlling them. These insights guide the industry’s efforts to minimize impact while maximizing efficiency.
Technological Innovation: Leading the Charge
Technological innovation is playing a critical role in emissions reduction. The industry is investing in cutting-edge technologies like remote sensing and advanced analytics. Tools like environmental software are not just conveniences; they are necessities in an evolving landscape.
Collaborations and Partnerships: Building Bridges
The pathway to reduced emissions in Canada’s oil and gas industry isn’t a solitary journey. It’s paved with collaborations, partnerships, and shared visions. Working with entities like Intricate Group, specializing in fugitive emission control, ensures that the industry benefits from collective wisdom, technology, and innovation necessary to make tangible progress.
A report by The Globe and Mail further illustrates the role of collaboration in shaping the industry’s future, particularly in emission reduction.
Educating and Empowering: A Knowledge-driven Approach
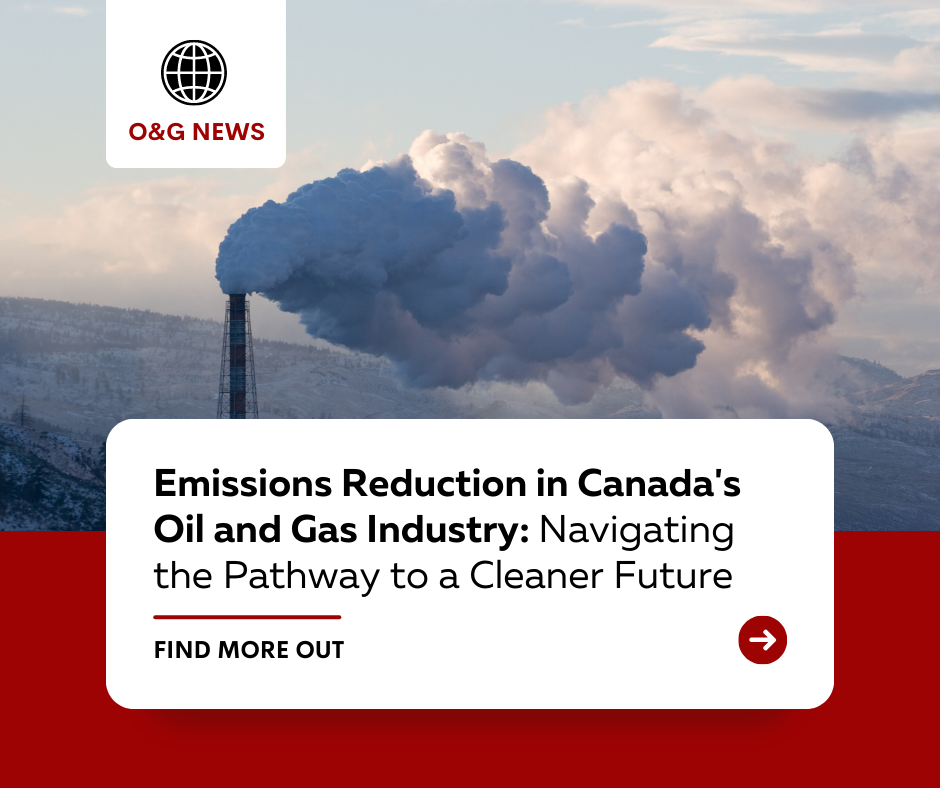
Understanding regulations, adapting technologies, and implementing the right strategies require comprehensive education and empowerment. Training programs, workshops, and information sessions are integral to ensuring that everyone in the industry is equipped to meet the challenges.
From Challenge to Opportunity: A Sustainable Journey
Canada’s oil and gas industry stands at the intersection of opportunity and responsibility. The task of reducing emissions, particularly fugitive emissions, is daunting but not insurmountable.
With innovative solutions like environmental software, clear adherence to regulations like MSAPR Multi-sector air pollutant regulations, targeted efforts to control fugitive emissions, and a strong focus on collaboration, the industry is forging a pathway to a sustainable future.
The efforts are not without complexities. Yet, within these complexities lies the strength and resilience of an industry that has weathered many storms. The journey towards emission reduction is filled with lessons and possibilities. It’s about embracing change, harnessing innovation, and fostering a collective commitment to a cleaner, greener tomorrow.
The story of Canada’s oil and gas industry isn’t just about fuels and profits; it’s about a legacy of environmental stewardship. A legacy that inspires and resonates, not just within Canada but globally. It is a vivid illustration of the capabilities, visions, and enduring values that fuel one of Canada’s most vital sectors.
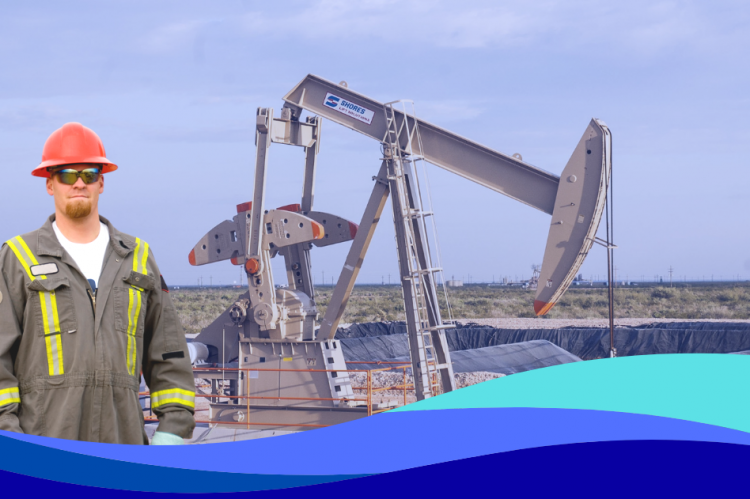
What are Energy Services Providers?
The introduction of the energy service provider in the 80s remains a crazy surge to the top when it comes to demand. service deliver a detailed of energy solutions including energy administration, testing and review, conservation, infrastructure and sustainability and maintenance. An energy service company (ESCO) is a company that offers thorough energy solutions to their customers, including auditing, redesigning and developing changes to the ways the client utilizes energy, the primary aim being increased efficiency.
Considering just this past year crude touched negative prices, we have since come-along way as energy report web sites are generally stating that petroleum prices will continue to go up through 2022. Regardless of this there still remains very much resistance from federal governments such as Canada, which have been making policies that conflict with the sector in attempts to get carbon neutral standing in the coming years. A good example of a dispute can be seen among the province of Alberta and the federal government of Canada. Alberta is without a doubt the biggest producer of oil in the nation while the federal government persistently obstructs development throughout the sector in that particular province by not granting pipelines and various high valued work.
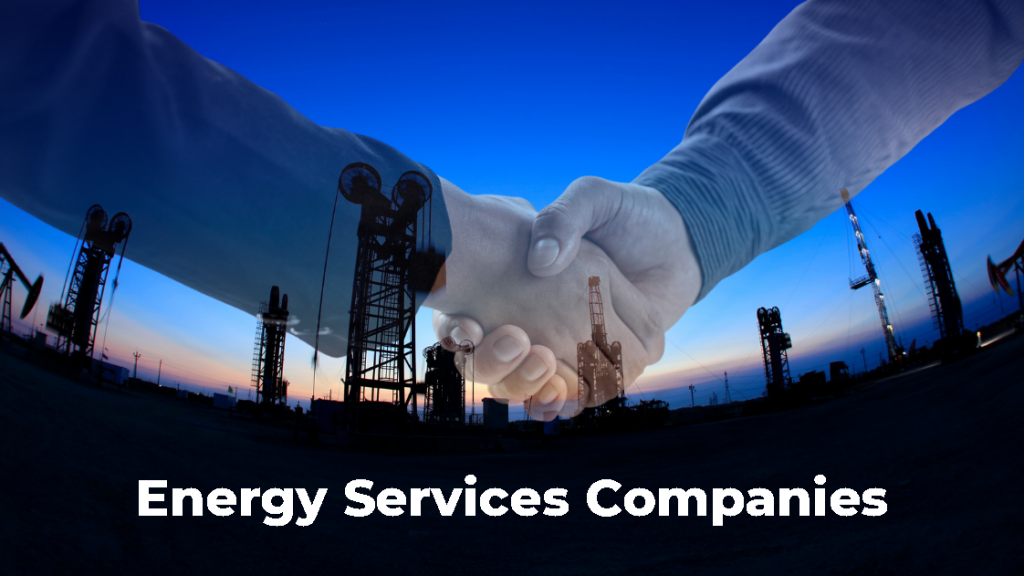
The ESCO presently is in constant flux and forever developing with new energy service providers being presented as the industry evolves post coronavirus. Technological innovation represents a crucial role in the energy sector and intrinsically energy services company (ESCOs) have changed to service this now technologically progressed vertical.
Energy services companies are fundamentally totally different from consulting engineers and equipment contractors: the former are generally paid for their tips and advice, whereas the latter are paid for the products. Deregulation of the energy sector in the 90s was the catalyst that propelled the rise of energy service firms. Now they are commonplace among many organizations which includes municipalities, school districts, industrial contracts and commercial verticals.
The stark distinctions involving the right led government of the U.S. and the Liberals of Canada is drastic in that one believes in wholesale deregulations whilst the other regulates the energy sector scare away large investors like Total.
With such a assortment of O&G service these firms provide, it is hard to list only a few while leaving out lots of other significant ones. but it’s worth noting that within this sector, innovation has performed a pinnacle role in assisting the sector evolution. A few other services include mobile steam services, water treatment, transportation, pipeline monitoring, automation, midstream & downstream solutions, energy cost savings and management and environmental consulting of government compliance regulation programs such as AMEP
The Alberta Methane Emissions Program is a three-year action which has a complete budget of $17.6 million that’s financed by the Government of Alberta through the Technology Innovation and Emissions Reduction (TIER) fund. The aim of the program is to encourage reductions in methane gas emissions.
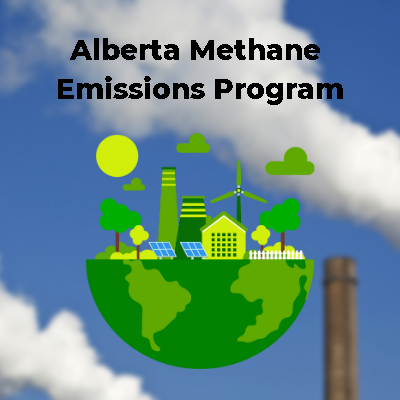
The goal of the program is to make it possible for the oil and gas sector in Alberta to reduce its pollution levels of methane, moreover to supporting the revising of government rules and regulations, decreasing the expenses sustained by the industry, and ensuring that recommendations are observed with respect to the detecting and management of methane. Financing for the Alberta Methane Emissions Reduction Program (AMEP) is supplied by the Technology Innovation and Emissions Reduction (TIER) Fund of Alberta. The AMEP program is maintained by the Delivery Agent Partnership (DAP), which had been established by the Carbon Management Canada (CMC) and the Sundre Petroleum Operators Group (SPOG). AMEP will serve as a world-wide showcase for environmental and monetary benefits that have been brought on by innovation in the private sector, research and development in academic facilities, and pro-active policy and regulation. This project is going to be backed by Alberta Environment and Parks (AEP) and completed in cooperation with the Alberta Energy Regulator (AER). Alberta Environment and Parks will as well make contributions to the AMEP budget. Environmental consulting services from energy services companies will assist you in meeting the regulatory requirements.
The AMEP focuses primarily on the reducing of methane emissions from oil and gas extraction activity in the upstream segment. Fugitive emissions consist of a proportion of total emissions, and a comprehensive comprehension of all input from this industry is important to ensure that industry and its regulators present the most effective management solutions possible. Throughout the AMEP, it’s quite likely that other sources of methane is likely to be identified; the information which is discovered will be used by the AEP to get a better knowledge of the larger variety of methane contributors, along with the strategies that are accessible to handle these emissions.
An additional energy service is the energy management consultant. For energy consultants as they are also called, the main focus is normally to save their customer in the energy consumption department. These service companies start with undertaking what is recognized as a baseline of initial energy assessment. Energy consultants use a defined start point which should be to conduct a total and thorough energy audit to be later utilized as a gage of future energy savings. The pros of operating closely with top organizational senior leadership is that when a commitment is required to be made its made then and there. This is precisely why energy consultants work along with and are accountable to, business administrators. The importance of the working relationship in between the energy consultant and the organizations managers can’t be downplayed given throughout any energy audit it’s important to have management conveniently available.
Field energy service providers organizations offer a wide array of solutions which include meter proving, sampling and analysis, electrical and instrumentation, construction, automation and controls and even software solutions. You don’t have to look very far to see the devastation created by COVID19. Tens of thousands of jobs in the energy sector were lost in the first half of 2020 throughout the US and Canada.
For the purposes of this article we decided to ask Ali Dibartolomeo senior executive of operations of Bloom Consulting what his thoughts were on the industry moving forward after the virus.
“The energy vertical has witnessed many hits through the years and if I’m to be genuine, even though this pathogen is damaging and in a wholesale way, the industry will return. Our business for instance has taken the past couple months to plan on how we expect to move ahead in 2021.”
ESCOs are usually privately owned companies, either independent or a component of a significant conglomerate, state owned, non-profit, joint ventures, manufacturers or manufacturers’ subsidiaries.
Degraded energy control technologies plagues a number of industry buildings in the United States Of America and this is commonly because of partially installed controller systems, excessive energy loss resulting from lack of insulation and out-of-date heating and cooling systems. This really is an additional reason why having an energy audit performed is significant so you’ll be able to then move to the next move by getting a expert energy consultant. The company of energy service can often mean many things but the one commonality between them all is the common objective of reducing energy expenditures and making current processes more efficient.
It is without doubt that we will be seeing a transformation, or an development per se, of energy utility firms whereas instead of selling just electricity or gas, utilities organizations will start to sell bundled services, which might include providers utilities didn’t considered before, solutions facilitated by smart meters and smart home technologies, like home protection, as an example, or monitoring aging adults. It has become widespread in Canada and the USA that energy providers are now providing bundled service providers like home phone, TV and internet but in reality there is a great deal of this going on in the B2B (business to business) side whilst public surveillance and security systems are also being supplied. We are now seeing the advancement and fusion of utility and service firms.
Now before you go thinking this means the end of energy solutions organizations I would like to stress that professional energy service providers organizations or those operating in the oilfields, are a modern necessity and can never be substituted by utility giants. While there is always the chance they could bring them more in house instead of outside independent organizations. Well that is the question on my people’s minds however it is without a doubt that energy service providers are resilient and most definitely will find means to adapt in this new world.

Energy Service Companies in a Post COVID Environment
The emergence of the energy service provider in the 1980s was nothing short of a wild surge up in the case of demand. Energy service providers cover a broad array of energy sector services. An ESCO is a company that provides specific energy solutions to their clients, which includes auditing, improving and developing changes to the ways the customer consumes energy, the definitive target being boosted efficiency.
Relating to the newest reports and headlines by energy media outlets, heading to 2022 we’re positioned to see historic high big oil prices. Considering though that several nations have promised to become carbon neutral in the years to come, this creates complications for energy generating countries. Alberta, a Canadian province, is a good example of this whereas the province produces the bulk of it’s oil reserves but the government continuously obstructs advancement of the industry through that province by refusing to approve projects.
As the world emerges from the gripes of the COVID we’re witness to the development of the ESCO. Technologies plays a sizeable role in the energy market and intrinsically ESCOs have adjusted to serve this now technically sophisticated field.

Typically energy service companies focus on decreasing energy expenditure and saving organizations on energy spending by a variety of ways which includes regulatory energy consumption and low priced rate agreements regarding energy consultants. With deregulation in the United States energy market in the ’90s, the energy solutions business experienced a swift boost. Utilities, which for a long time experienced the shelter of monopolies with guaranteed revenue on power-plant assets, now were forced to compete to supply power to several of their biggest clients. Three years in to the Trump presidential term we’ve observed a considerable sweeping deregulation in the energy sector which obviously benefits energy service companies.
A worthwhile assessment between the United States Of America and Canada displays the contrasting variances with a deregulating government like the USA is at the moment, and the progressive government of Canada. If truth be told, as of writing this article Total has revealed they’re going to be writing off over $6 billion in Alberta oil sands resources in Canada.
With such a assortment of OandG services these companies provide, it’s difficult to list only a few whilst excluding lots of other important varieties. but it’s really worth remembering that amongst this industry, technology has played a top role in helping the sector advancements. A couple other services include boiler rentals, water treatment, transportation, pipeline screening, automation, midstream & downstream solutions and leak detection and repair (LDAR).
Consulting and negotiating energy costs is an additional in-demand service as energy management companies have-been springing up all over Canada and the US to fill the demand for low cost rates. The primary focus of energy consultants is to always save their customers dough by reducing energy rates and making existing functions more cost effective. The first step any energy management firm will carry out is a full and comprehensive energy audit in an effort to recognize a starting base line. Working with a recorded starting position after a company executes its energy audit is fundamental. Organizations that hire energy management companies realize the relevance of these reports by these energy service firms and thus often work closely with each other. The importance of the close working relationship amongst the energy consultant and the organizations top executives can not be understated given during any energy audit it’s vital to have corporate leaders readily available.
Some of the service providers these firms perform might include things like turnarounds, fabrication, environmental impact studies, meter proving, mobile boiler trucks, transport and others. You don’t have to look very far to see the devastation created by COVID19. Tens of thousands of jobs in the energy sector were lost in the first half of 2020 throughout the US and Canada.

We spoke with Broderick Culbreth, an operations executive with Barton Energy service providers and here’s what he had to say.
“While it’s correct that we’re seeing a paramount shift within the energy sector since COVID, we’re also experiencing the introduction of new technologies and standards of how we behave ourselves on the job. Energy service providers is definitely taking a blow while on the other hand will re-emerge sturdier than ever.”
ESCOs are privately owned firms, either independent or an integral part of a large conglomerate, state-owned, non-profit, jv partnerships, manufacturers or manufacturers’ subsidiaries.
Market guidelines and government and industry regulations are the prime focal point to which all energy service providers must function. They are experienced in refining and simplifying the entire project to provide maximum efficiency and energy savings.
Long ahead of COVID we’d already began to see utility firms begin to reinvent themselves and make themselves more pertinent by grouping solutions you may not of previous thought they could offer. Things like internet providers now offering bundles with TV and home phone on top of the internet service. In Canada we commonly see energy providers partnering with government so they’ll further increase their scope with customers which includes the principal natural gas company in Canada called Enbridge, Enbridge has worked diligently to grow their service and products to capture more of the energy consumer sector. Basically as this happens, energy providers become energy service organizations offering a broad range of solutions versus concentrating on just supplying it.
You’re likely asking yourself that if this indeed is taking place then would not that make independent ESCOs obsolete? That said we hope that 2021 brings much prosperity to the energy sector and we can look back at 2020 as a year of lessons.
The Role of Energy Service Providers Across North America
Probably the swiftest growing segments of the entire oil and gas markets is energy service. An energy service company (ESCO) are organizations that provides a broad range of energy solutions which include plans and implementation of energy savings jobs, retrofitting, energy resource efficiency, energy infrastructure outsourcing, power creation and energy supply, and risk assessment. An ESCO is a company that boasts specific energy solutions to its clientele, this includes auditing, redesigning and applying adjustments to the ways the consumer consumes energy, the main objective being considerably improved efficiency.
After their inception in the 1980s, energy service firms have evolved and expanded. Since COVID enveloped the world we’ve seen probably the most radical changes to this sector while trying to remain relevant. One other version of energy service providers was the technological part where sophisticated measuring instruments and other diagnostic devices have emerged as common in this swiftly developing industry.
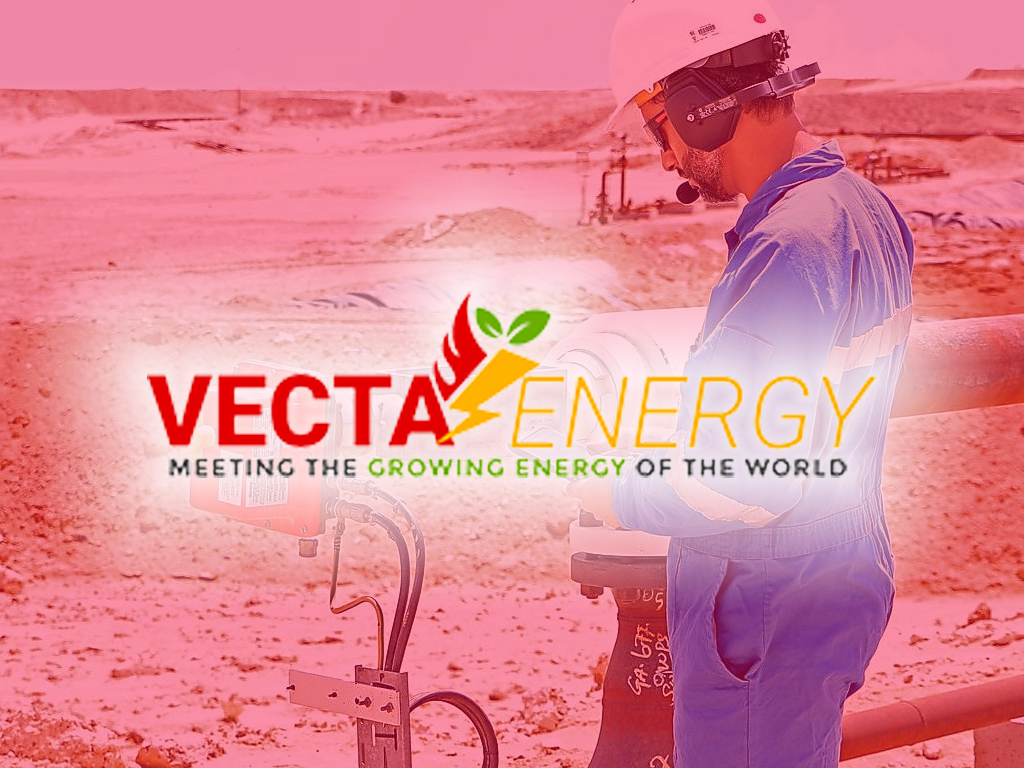
It’s somewhat obscure outside the sector but energy costs and efficiency can be much better and the reality is that is the principal challenge for most energy solutions company. With deregulation in the U.S. energy markets in the nineties, the energy providers business enjoyed a rapid rise. Utilities, which for a long time valued the shelter of monopolies with certain earnings on power plant investments, now must compete to supply power to a number of their biggest customers. At the present time we are witness to probably the largest deregulating governments the U . S . have ever seen which is only improving with recent remarks from the Trump Administration made in Texas this past week.
The huge differences in between the right leading government of the US and the left of Canada is drastic in that one trusts in wholesale deregulations whilst the other regulates the energy sector so much they hinder progress.
Each ESCO differs in their own technical expertises while others address the entire spectrum of services which includes measurement & regulatory, project planning, integrated solutions, commissioning & startup and more. A few other services include water treatment, transportation, pipeline tracking, leak detection, midstream & downstream solutions and energy savings and administration.

Energy consultants are on the increase as prices fluctuate we see a demand for energy consulting agencies to obtain cheaper energy prices. For energy consulting firms as they’re also referenced as, the chief focus is always to save their clients in the energy expense department. The initial step any energy management firm will undertake is a complete and specific energy review in order to establish a starting base-line. What this does is it develops a quantifiable start line in which everything moving forward could be assessed from to establish energy savings efficiency. Organizations that hire energy management organizations understand the usefulness of these reports by these energy service organizations and subsequently often work closely together. Whilst energy management firms function separately of the organization employing them, it is a reality that energy consultants work intimately with officials for a multitude of reasons.
Energy solutions firms encompass a wide array of different service and products. You don’t have to look very far to see the devastation created by COVID19. Tens of thousands of jobs in the energy sector were lost in the first half of 2020 throughout the US and Canada.
For the purposes of this blog post we opted to ask Mohammad Michand senior executive of operations of Bloom Consulting what his thoughts were on the industry moving forward after the virus.
“The energy market has experienced many strikes throughout the years and if I’m to be frank, although this pathogen is harmful and in a wholesale fashion, the market will rebound. Our corporation as an example has taken the past few months to strategize on how we need to progress in 2021.”
Turnaround providers is another component to the variety of services by energy service companies that involves project administration for the duration of operational turnarounds of plants during maintenance. This type of service can cover a number of other providers within it which includes regulatory, measurement, testing and others. Depending on the scale of the job, these jobs commonly last from 2-4 weeks.
Market guidelines and governmental and market regulations are the fundamental focal point that all energy service companies must operate. The company of energy service can mean many things but the one commonality with them all is the common objective of lessening energy expenditures and making current systems more economical.
Energy utility providers began to evolve even before the pandemic when they began to see the intrinsic value in grouping different service providers together like Internet, TV and phone. But beyond that you now see utility firms also offering home and commercial alarms and smart home solutions. In Canada we commonly see energy providers partnering with government so they can further grow their reach with customers which include the principal natural gas company in Canada called Enbridge. Enbridge has worked diligently to diversify their service providers and products to capture more of the energy consumer market. Effectively as this transpires, energy providers transform into energy service firms offering a wide variety of services versus concentrating on simply providing it.
You’re most likely asking yourself that if this really is occurring then would not that make independent ESCOs outdated? In closing you should note that energy providers is a growing company that incorporates a myriad of different job specific service providers whether in the oilfields or on the rig.
Meter Proving & Testing: A Deep Dive
Quite simply, meter proving where the precision of a meter is analyzed. The facets for Meter Proving also, the expected outcomes can change per the diverse kinds of meters using unique functions. For instance a propane gas meter prover checks the correctness of the propane meter. Lots of meter provers choose to confirm their results against a preset array as shown in the guides..
It is now essential to get aware of that though meter proving and meter testing could very well to-be the same thing, they are not and the dissimilarities are critical to get aware of also.
When a skilled professional is validating the accuracy of the meter this is whats called meter proving. Things like verifying the appropriate amount of disbursement to the meter outcome itself. Meter proving is done by comparing the service meter versus accredited prover (master meter, dynamic or tank prover) which is traceable to a national meteorology institute similar to NIST. Proving meters of hydrocarbon is very common with pipelines. In lots of cases provers will coordinate with meter station personnel to compare and contrast outcomes.
There are several design requirements for calibration systems used by energy management companies. These can include, but are not limited to volumetric methods, gravimetric methods, and master meter comparison. These methods can produce results with a doubt of better than 4-to-1 as weighed against the meter become tested.
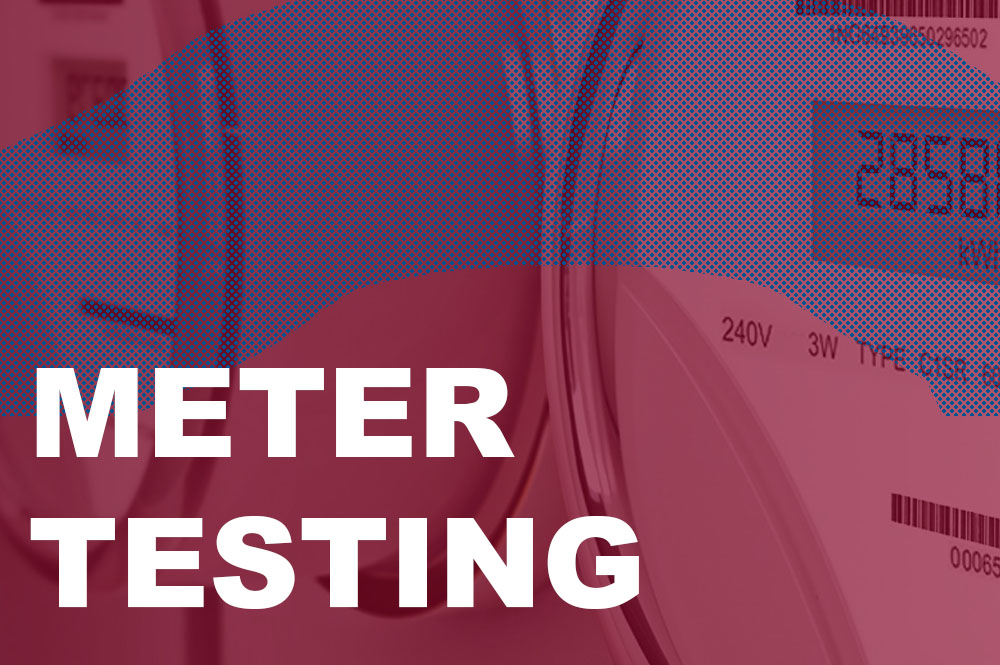
In addition, there are requirements that govern and incorporate the calibration system that is entire. NIST and ISO 17025 define criteria and needs with varying amounts of complexity for calibration facilities and procedures. The National Institute of Standards and Technologies, or NIST, defines requirements for traceability that real time utilizing the lab that is individual maintenance or self-compliance. ISO 17025 is a more rigorous, third-party official certification. This standard takes into account the whole calibration system and produces metrics for the calibration rig elements, administrative systems for process operations, workers proficiency, and paperwork giving support to the traceability and total dimension doubt for the calibration center that is entire. ISO 17025 standards ensure the level that is greatest of confidence in accuracy and repeatability.
Curiously, for longer than 100 years the standard continues to end up being what is acknowledged as “bell provers” which is certainly also littered with insecurities on to on its own.
And then we have got the prevalent gas meter proving expert whom checks and confirms gas meters. Municipal and public works are without question the most common employers of meter provers.The process wherein meter proving contractors examine the correctness of a meter is by passing air through after which evaluating those outcomes to the meter’s own interior displacement. After that is complete the prover (meter) then takes the data he/she documented in the percentage of air moved to compared to the value depicted on the meter’s own.
The bell is ultimately a vertical internal container having an external protective exterior. There are two layers and while the external layer is normally loaded with oil, the interior layer is known as the bell. The fluid could there be to behave as a air-tight seal for testing. Bell provers are generally counterweighted to provide positive pressure through a hose and valve attached to a meter. We regularly see rollers on the bell that allows for soft linear motion without likelihood of ruining the pressure level created by the bell seal moving.
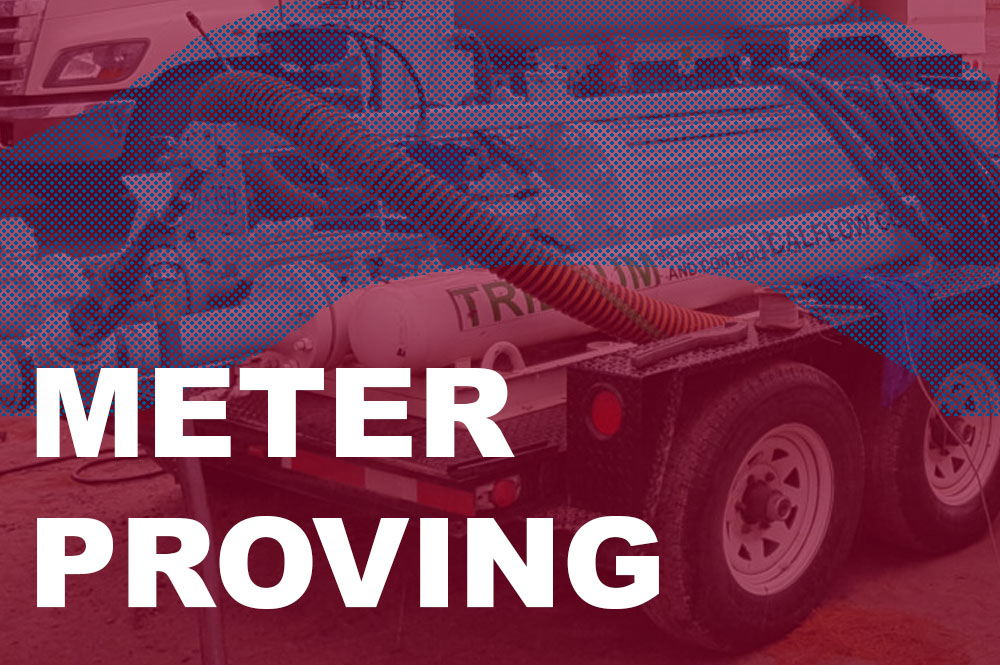
Errors in proving by operators is believe it or not common and has to be regarded and adapted. Temperature inconsistencies involving the bell air, meter and binding hoses could explain many meter proof inaccuracies. There are a laundry list of things to go wrong that has to be regarded like human error and mechanical issues.
As we earlier revealed, each gas type features its own system of meter testing. Natural gas for example demands a couple of visual inspections just before the PACs are used. There are a plethora of other testing methods outside the scope of this article. One exception nonetheless is the hardly ever utilized orifice meter testing which does require checking against primary devices against the field data obtained from field provers.
There you have it, that’s exactly how meter testing is carried out and the subtleties of the work involved by meter provers in the field and inside machine-controlled devices.
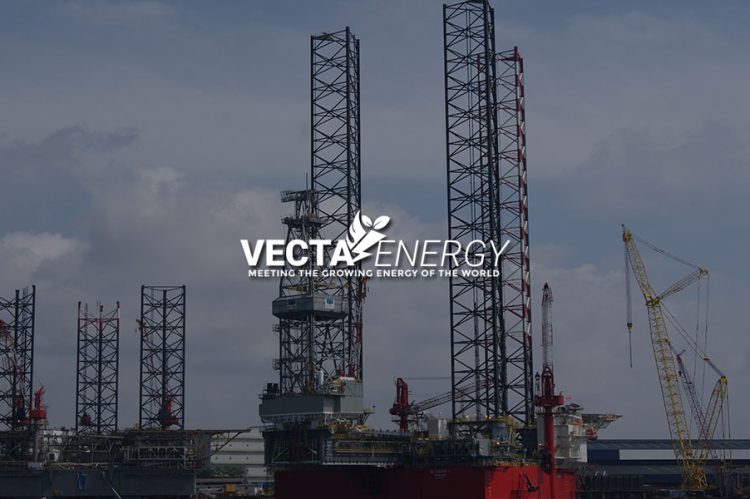
3 major types of offshore oil rigs used today
In the past, drilling was only limited to coastal drilling. But now, due to technological development, it is possible to drill in great depths anywhere in the sea. Here are the major offshore oil rigs used today.
Fixed platform
These rigs are placed into the seabed directly. These are tall steel structures that rise up. There is a surface deck where drilling modules are available. The crews also live here. These rigs can drill up to 1,500 feet deep. It is very expensive to construct these rigs. So, unless your survey results show the possibility of a high amount of oil reserves, it is not worth building these rigs.
Floating production system
This is an unconventional method of drilling oil. It is used when companies need to get oil from deeper into the ocean. A part of this system floats on the water and part of it is submerged under the water. It can be used to dig oil from up to 6,000 feet below the surface of the water.
Jack-up rig
These are used for shallow water drilling. So, if you have found a small offshore oil deposit then this type of rig is appropriate. These rigs have floating platforms that are towed by barges. It has support legs that are lowered into the seabed and so the rig comes on top of the water surface. The legs can be lowered up to a limited depth.
Continuous improvements are going on in the development of offshore rigs. Companies now have to dig deep down to extract oil, so they need a more sophisticated system and latest technology to locate the source of oil. Bringing up the oil to the surface can be very challenging. There are lots of risks involved. Oil companies must learn how to perform these tasks safely.
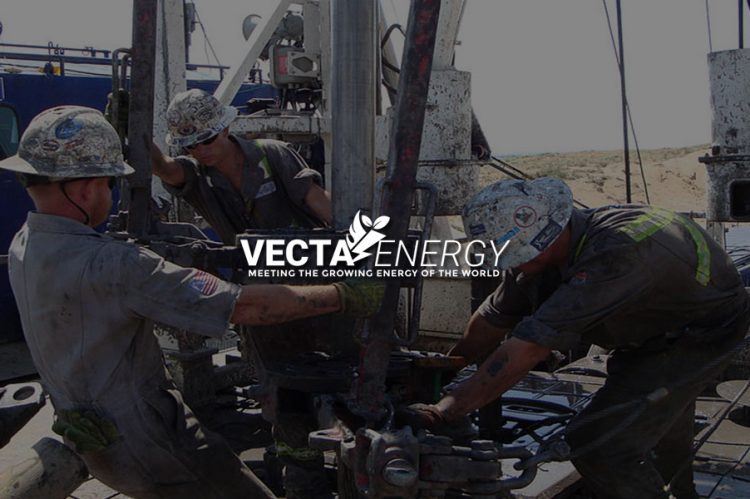
4 reasons to work in the oil and gas industry
It is expected that oil production will almost double in the next 15 years. So, there are lots of opportunities out there. Choosing a career in this industry will be a smart decision for many reasons.
High demand
There will always be demand for oil and gas. No matter what the political or economic situation is of a country, the demand will never diminish. So, there is a big market out there. New companies have entered the market creating more job opportunities.
Good pay
The pay is really good in this profession. Offshore works, in particular, involve lots of risks so employees get bonuses and other facilities. So, you will get high financial security by working in this industry.
Flexible working hours
Flexible working hours are available for both onshore and offshore employees. If you work onshore you will be able to get weekends off. If you work offshore you will probably work for six weeks and then get the next six weeks off. You can work on any 12-hour shift.
Opportunities for growth
You will get lots of opportunities to move your career further. You will get continuous on-the-job training which will help you to acquire new skills. The more you gain knowledge and experience; the better is your chance of going up the ladder in this industry.
There are always job opportunities in the oil and gas sector. If you have the right skills you will be able to have a good career in this highly demanding sector.
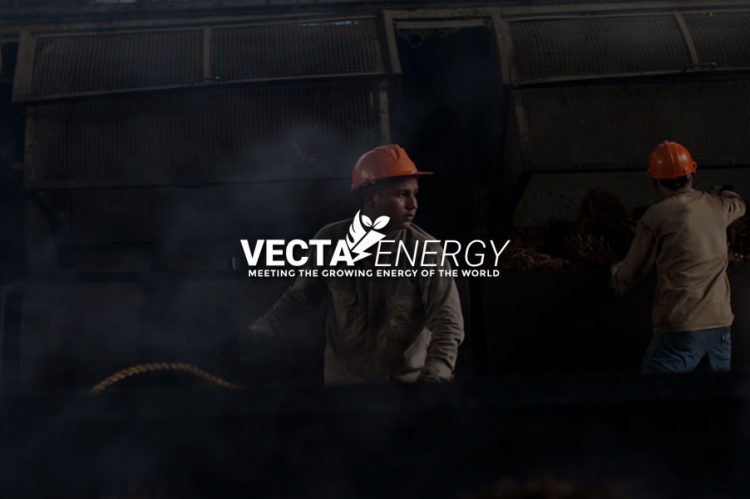
4 reasons why quality control is important in the oil and gas sector
Producing oil and gas is a very risky operation. There is a risk in every step of the process from exploring energy sources to transporting the final products to the consumers. Quality control is essential in every step to ensure that the product quality is good and no harm is caused to the environment. Here are the top reasons for having strict quality control in this sector.
Less environmental damage
well’s complexity is directly related to the environment in which the well is being drilled and to a multitude of factors that can affect performance, safety, and the lifecycle and integrity of a company’s oil and gas assets. A well-thought-out Quality Management System (QMS) developed by an experienced team of engineers, quality experts, and inspectors can save an organization time and money and mitigate risk. This is precisely why a highly skilled technical team whose experience is rooted in some of the most complex and critical wells in the world is a team that is the most qualified for the job.
Gas and oil drilling
Gas and oil drilling operations can cause direct impact on the environment. A highly skilled team of technicians and worker must conduct these operations. The work is very sensitive. Any mistake may cause a huge negative effect on the environment. So, quality control is extremely important in case of gas and oil drilling operations.
Getting ISO certification
Having an ISO 9001 certification proves that the company has a high quality management system. It is very difficult to obtain this credential as the company has to demonstrate quality process approach and other criteria. ISO 14001 certification is also necessary for oil and gas companies. This certification indicates that the company has an environment system in place. The company must continuously monitor the environmental impacts of their operation if they want to obtain and maintain this credential.
Safety of the workers
The working environment of oil and gas company is risky. The work itself is very complicated and has a high chance of causing accidents if not carefully done. The companies must incorporate safety issues in their design and manufacturing phase. Oil and gas companies must obtain OCTG certification which proves that they follow international standards in their every stage of operation. So, this protects the safety of the company’s employees.
The major oil and gas companies have a separate department for quality control. The quality control and assurance team ensure that proper standards are maintained at each step of their operation. This ensures quality end products to be supplied to the consumers.